
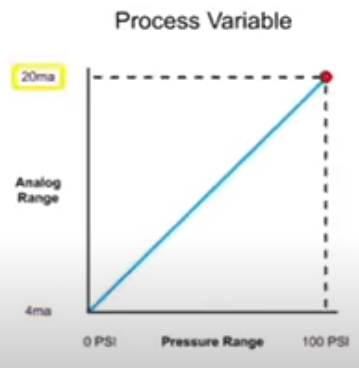

The PID Controller block now tracks its own output, which is equivalent to control mode.
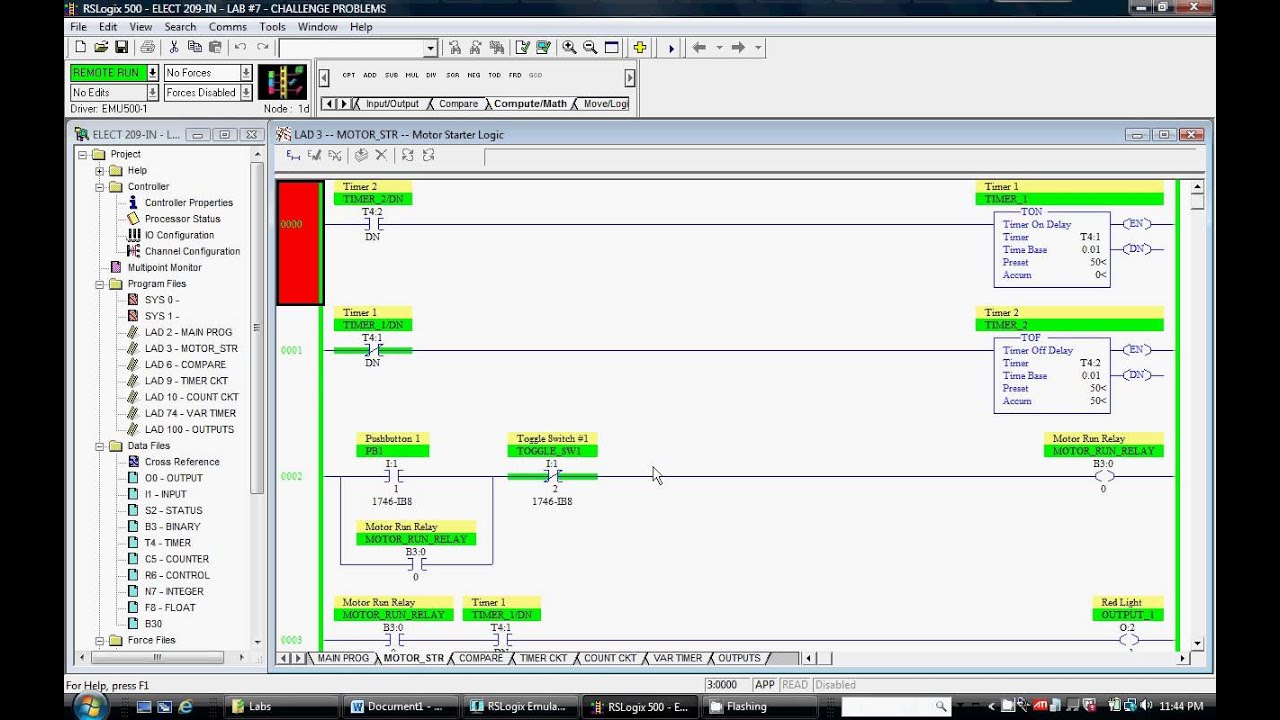
#RSLOGIX 500 PID MANUAL#
When control transfer occurs, therefore, the PID Controller output will be approximately the same as the manual control signal.Īt time t = 150, Switch 1 switches, directing the output of the PID Controller block to the plant input and the PID Controller block's tracking input. This allows the output of the PID Controller block to track the manual control signal during the manual phase by adjusting the PID Controller's internal integrator. Switch 1 determines which signal feeds the plant input and feeds the tracking port of the PID Controller block.Īt time t = 0, Switch 1 directs the manual control signal to the plant input and the tracking port of the PID Controller block. In addition to enabling tracking mode for the PID Controller block, a switching mechanism is needed to achieve the control transfer. įigure 3: Under-mask view of the PID Controller block with tracking mode.
#RSLOGIX 500 PID HOW TO#
For more information on how to choose this gain, see Reference. The inverse of this gain is the time constant of the tracking loop. To activate signal tracking, go to the Initialization tab in the block dialog select Enable tracking mode, and specify the gain Kt. MO In the program I mentioned, there is a PID that its CV is not used in nowhere in the. SO or this kind of variable is only active in Manual mode and first we have to set the BIT. To achieve bumpless control transfer, the PID Controller block must be in tracking mode when the plant is in the manual control phase (open-loop control), and in control mode when the plant is in the automatic control phase (closed-loop control). I am analyzing a program made in RSLogix 5000, specially de PID loops, I have some questions: This is the first: In AUTO mode a PID can control an Output, using only the variable. In tracking mode, however, the block has an extra input that allows the PID block to adjust its internal state by changing its integrator output so that the block output tracks a prescribed signal feeding this extra input port. In control mode, the PID Controller block operates as an ordinary PID controller. To support smooth control transition, the PID Controller block supports two modes of operation: a tracking mode and a control mode.

Hardware design that does not include a PLC for electronic circuits: /r/AskElectronics.PLC internship, employment and education questions.Homework help but make it clear it's homework.This sub is dedicated to discussion and questions about Programmable Logic Controllers (PLCs): "an industrial digital computer that has been ruggedized and adapted for the control of manufacturing processes, such as assembly lines, robotic devices, or any activity that requires high reliability, ease of programming, and process fault diagnosis." On topic subjects
